Project Management
Note: The following section is academic and exists as a small blueprint for some early impressions made about entrepreneurship and the importance of systems and or the “Franchise Model” to support scalability of knowledge and preserve integrity definitions for product and services. The section is intended as a personal reminder to some creative ideas or interesting “problems” that have yet to be fully explored in my career and anchor my academic interests at-large.
AGT Water Systems
Stephen Covey’s Time Matrix - “The 7 Habits of Highly Effective People”
Introduced to Absolute Graphic Technologies (AGT) in Corona California through the advisory board of Webber Automation, a new venture AGT Water Systems was starting first production as a subsidiary to AGT. Transferring to AGT Water Systems on the basis of project management and engineering, the company had a lot of work ahead to establish functional operations. Recognizing project management was premature, a heavy focus to learn inherent processes followed: purchasing, quality assurance, unit assembly, inventory management, BOM’s, part numbering, vendor management, and operating procedures of their ERP software, Made2Manage. Being responsible for the first data entry on their ERP system for AGT Water Systems eventually combed me into being the point man for all procurement and production directives. Initially I was put into the driver’s seat for procurement needs, which provided better understanding of materials and the work being undertaken. I appreciated the focused attention of purchasing needs to become familiarized with the unit and cash flow demand, driving initial meditations on project management concepts.
The first manufactured system was the 3,000 barrel/day water processing unit called EAGT3K. The original documentation available was a handful of 2D sketches and a flow diagram showing process. Collectively, the construction process of the EAGT3K system was undocumented and no operational structure was established. Experienced fabricators and electricians were able to dissect the original concept drawings of the system and produce the first prototype which was launched 3 months past the deadline. Understanding the nature of start up constraints, it was clear that design for manufacturing was an expensive undertaking AGT recognized as valuable, however not critical to deployment of their first functioning unit. In the balance of different personalities and company objectives towards upscale the first step was attending to urgent tasks and shaping the data and scope toward the planning and eventual appointment of tasks which did not exist previously on basis of project management or design for manufacturing.
Through insight of procurement and direct management of the ERP software, I was educated on company wide process and communication through formal and informal channels. My use of time had pros and cons, as experiences company abroad fed into analytical thought on process efficiencies, employee motivations, culture, expectations for change, cash flow, functional capacity, and general management, I had stretched my time availability. The presumptive goal was that by the start of the school season, enough experience and information would have been obtained to lay the foundations for project management and the analytical role which was initially proposed. Little did I know about the lack of information of the EAGT3K system to facilitate a constructive project management campaign as it was still a prototype phased production. The broad experience base about AGT’s processes or lack thereof preached much larger problems and restructuring needs before project management could ever function in its’ full capacity. First we would have to define the project, and AGT Water Systems was all still too young in the conception of the EAGT3K system design. Beyond this, the ecosystem of AGT was crucial to understand, reinforcing the value of my work abroad thus far. Some senior managers recognized the supplemental support to roles like purchasing, QA, and physical assembly as valuable experience to qualify for the potential role of analytics/project management. I struggled to separate time between the urgent and not urgent tasks. All the potential dwelled in the “not urgent,” while if not all the responsibilities I acquired were “urgent,” (Purchase orders, QA, Part Numbers for new materials, Quotes, Payment Confirmation/Approval, Vendor Setup). Company wide, the fire fighting dilemma existed. I had ascertained a portion of my time daily to always be reflecting on matters that could make considerable difference in the operations but wasn’t acting on them. It dawned on me this wasn’t any different from Stephen Covey’s “The 7 Habits of Highly Effective People,” who dissected people’s use of time with a matrix.
How was I going to afford the time to carefully quantify my observations, develop the means to share my ideas, and then drive the critical changes? Past working experience had taught me that it was possible for a senior manager to not recognize employee efforts to digest and quantify innovative solutions nor appreciate them. Other company personnel of AGT had seen my energy spike to assist with changing the organization but felt the efforts to make change would fall onto deaf ears as their efforts at once had. I didn’t have a way to judge the validity of their comments, but it warranted caution to how much outside time/effort I would spend to share ideas based on interaction with the organization. It seemed that there was safety in just being a helping hand for already existing tasks and needs rather than spend my time analyzing. Some ideas were very discouraging to introduce because the plans were so top heavy on support from powers above that really it wasn’t even my place to be driving the change. I already had spread myself thin, but taking a personal interest in large scale company ideas and methods was a conflicting interest. A side of me recognized I was an upcoming student, I also was brand new to the team, and my role was undefined to a degree which had grey zone of what I should/could be doing. The other half of me was that I loved this sort of thinking. An outside discussion with a mentor made me recognize the importance of treading lightly to acknowledge personal limitations, remember true goals, and the all-inclusive burden decisions have on time.
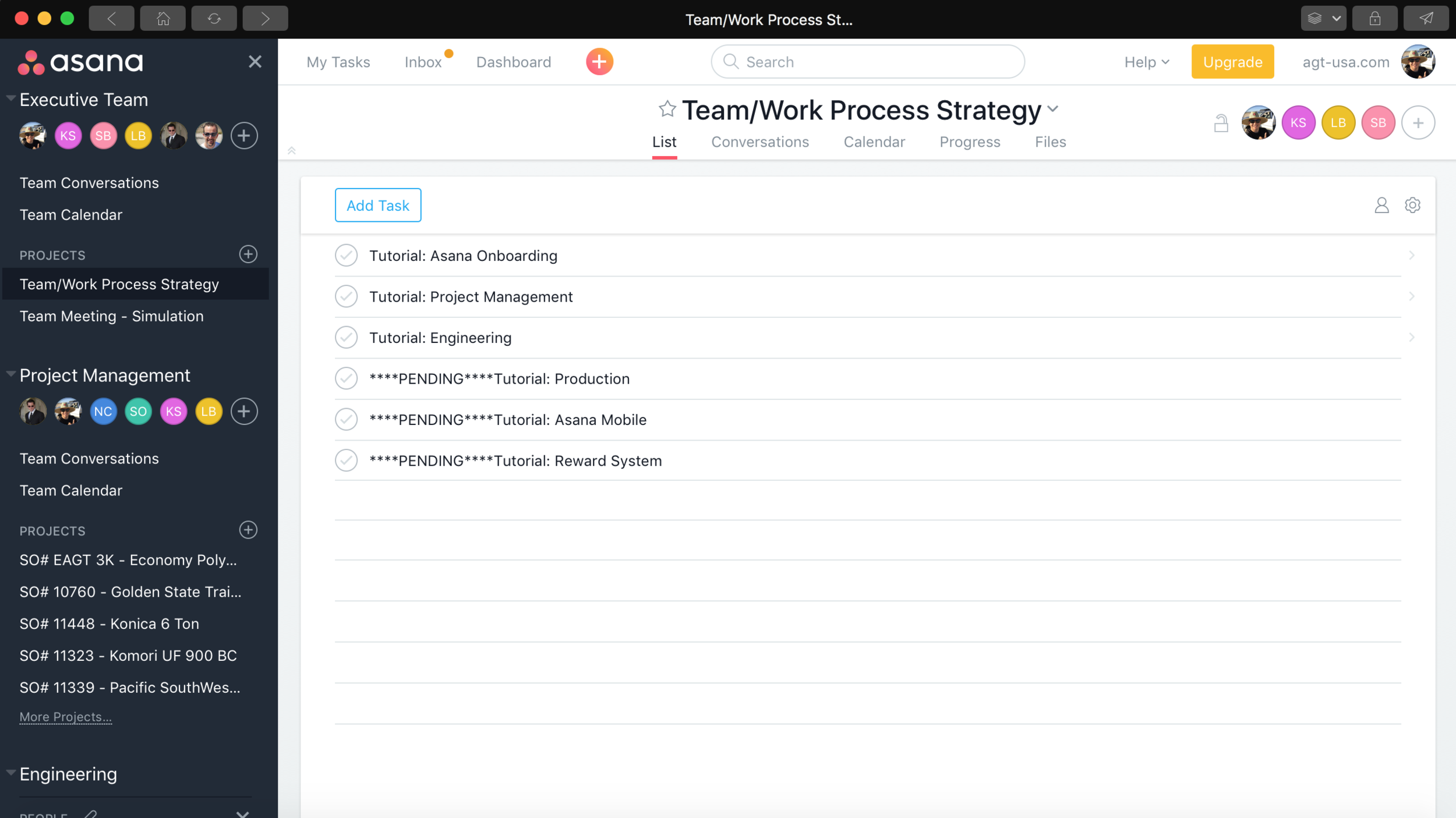
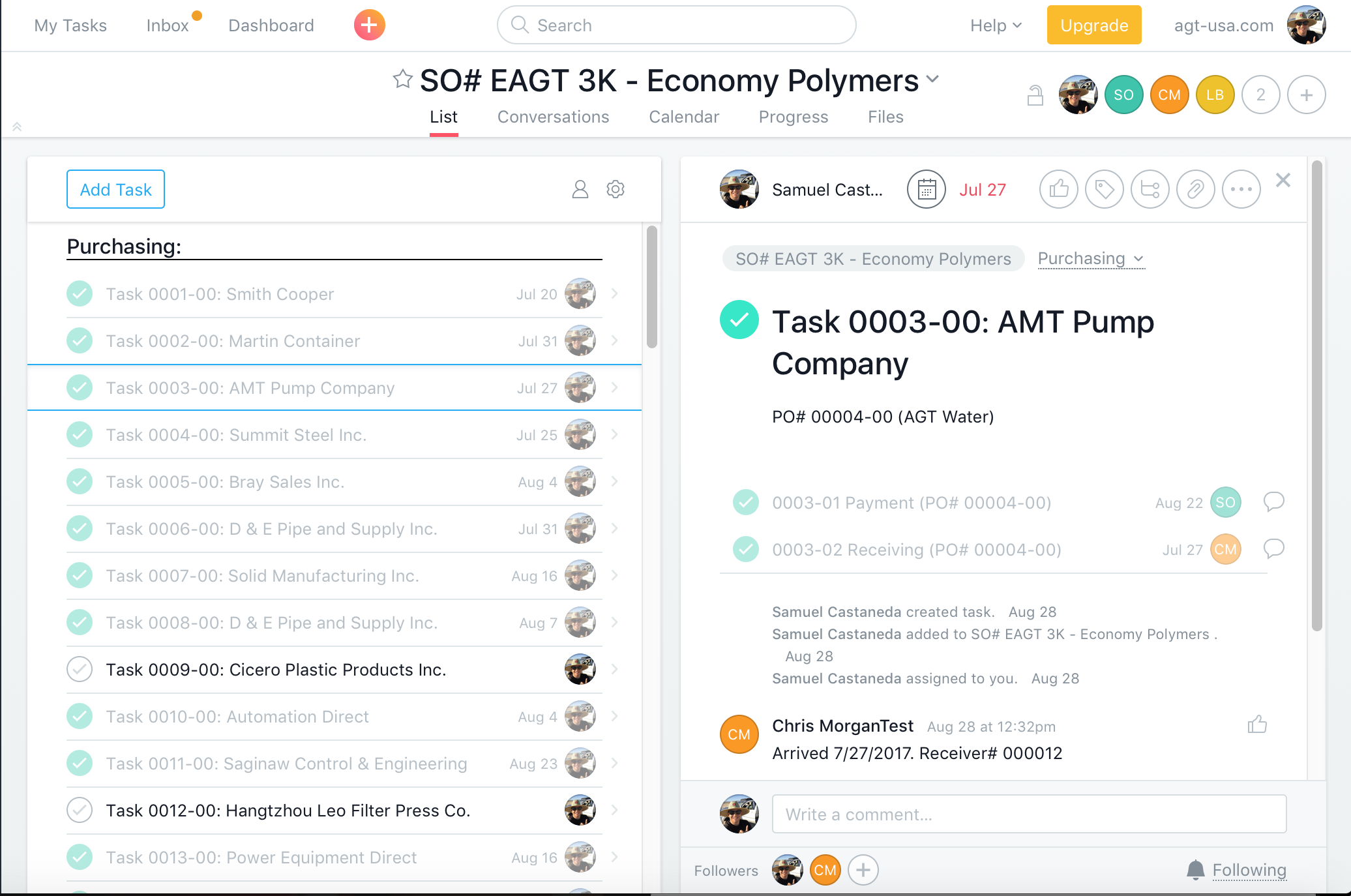
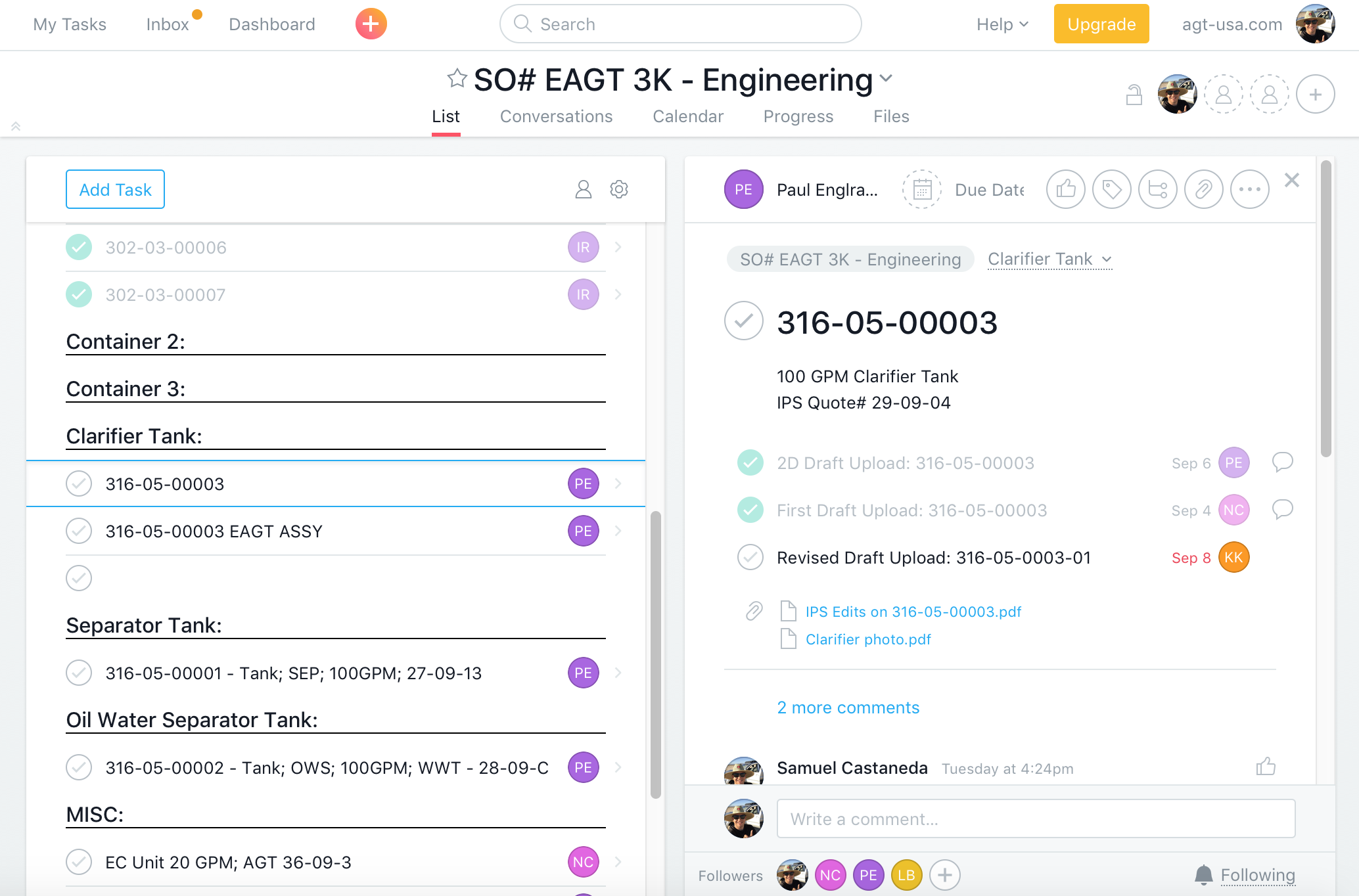

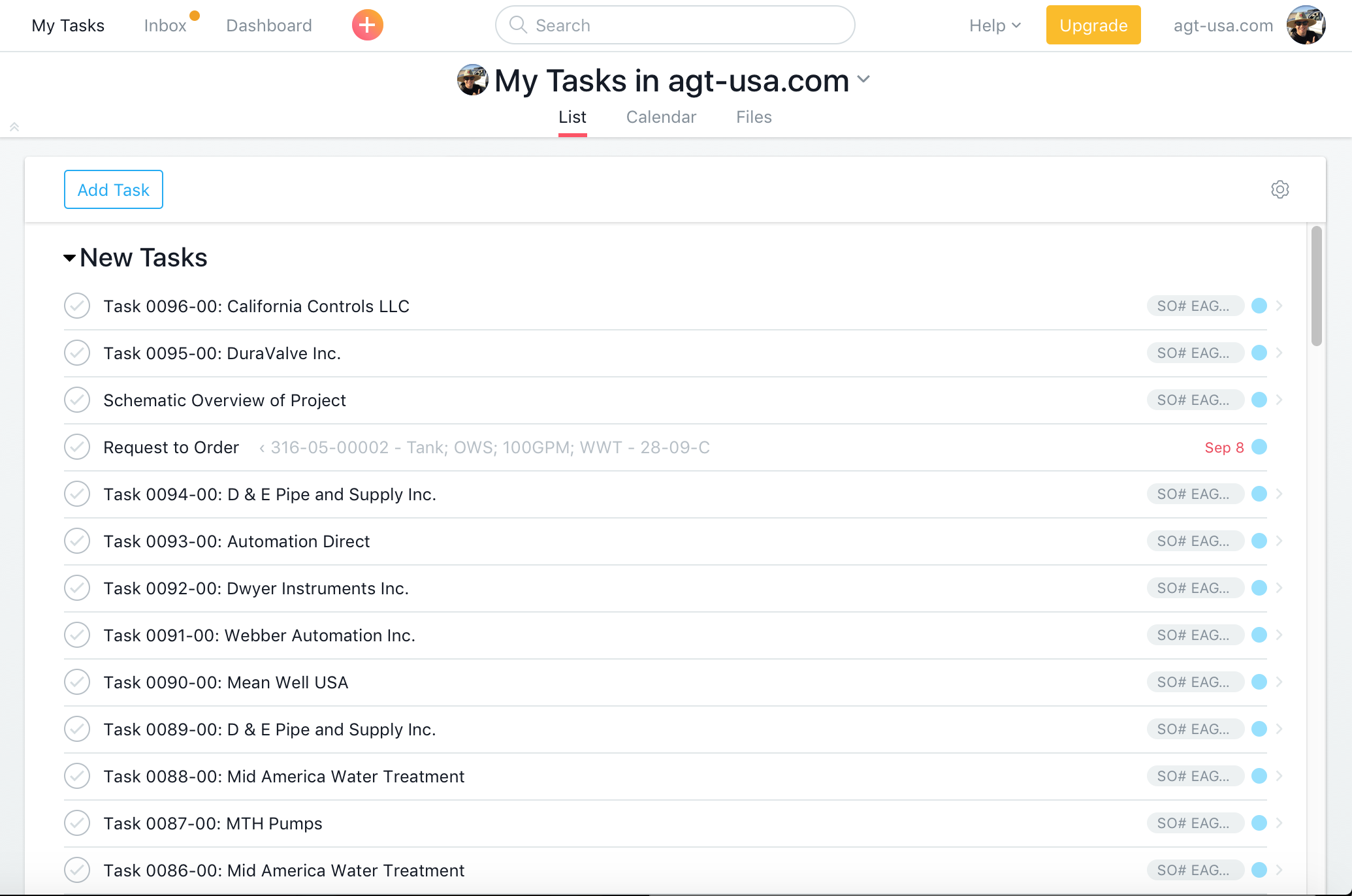
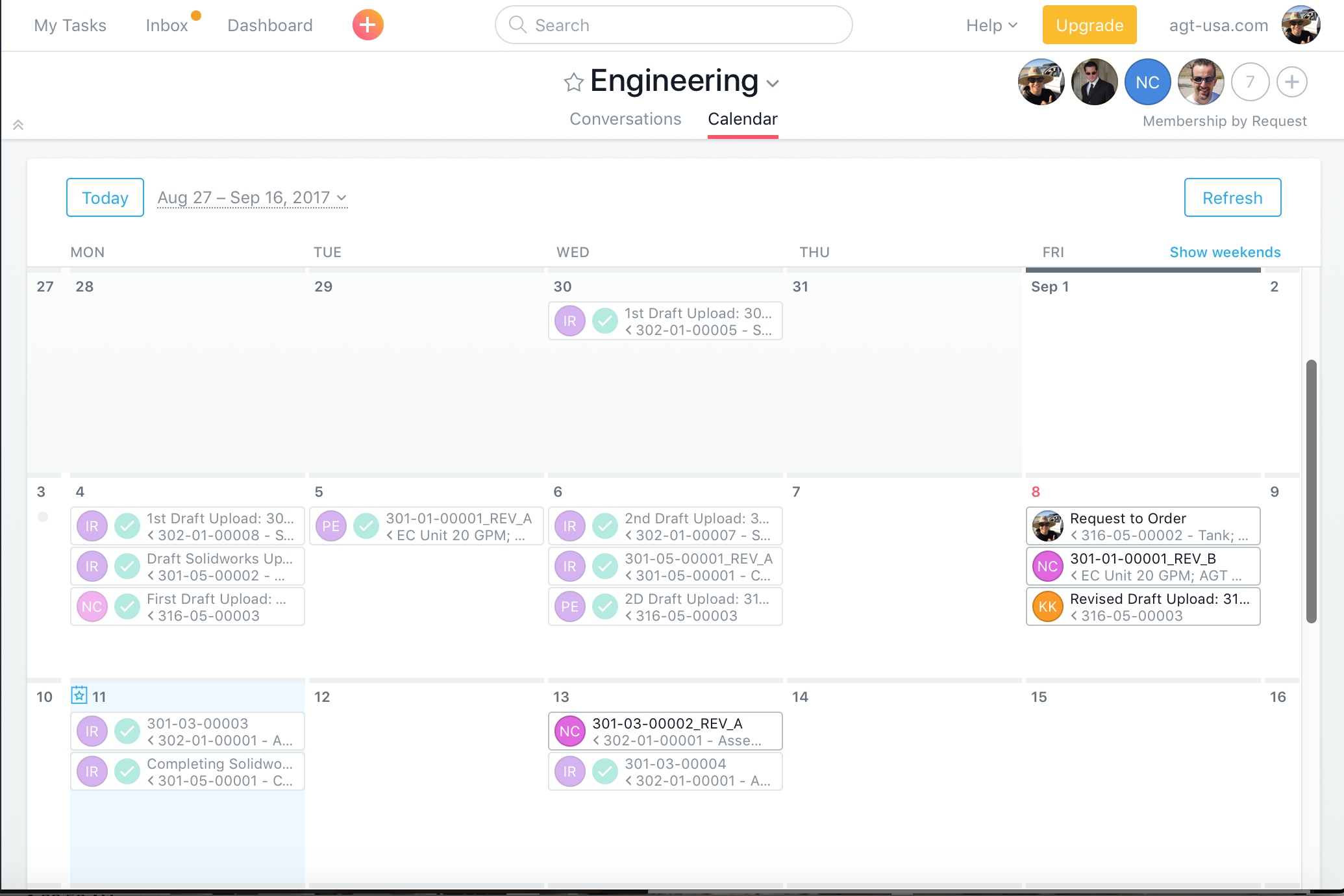
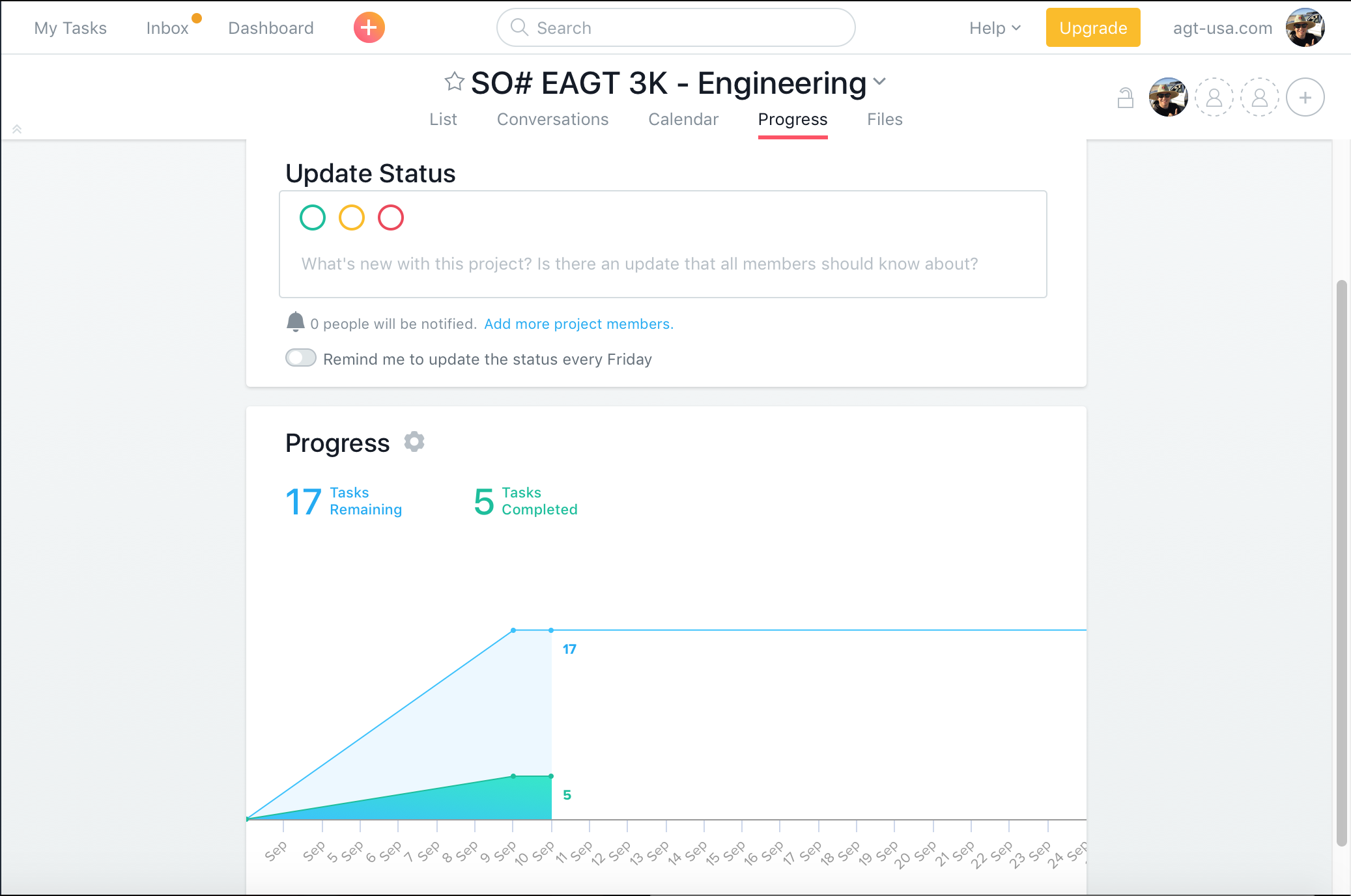
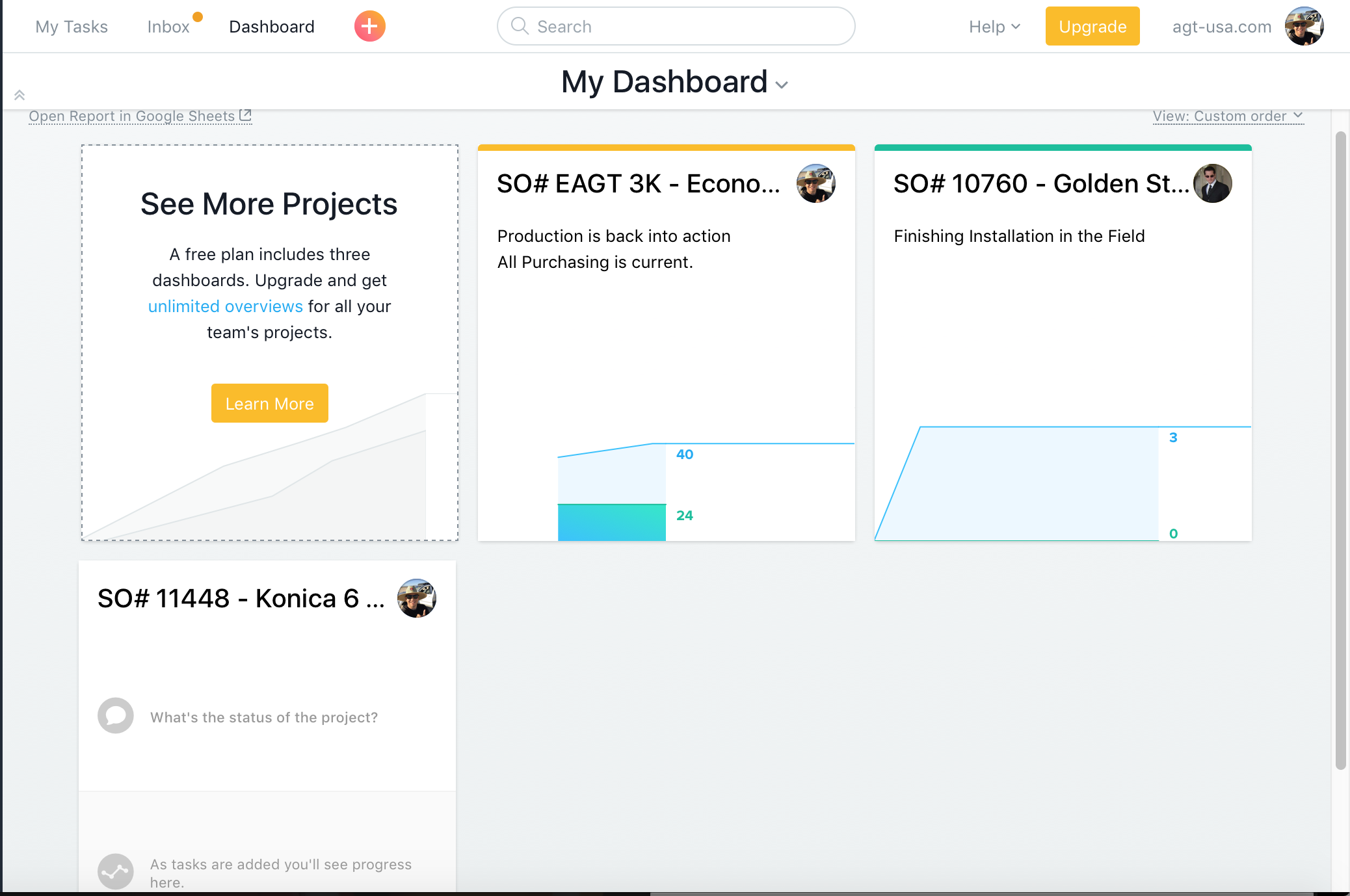


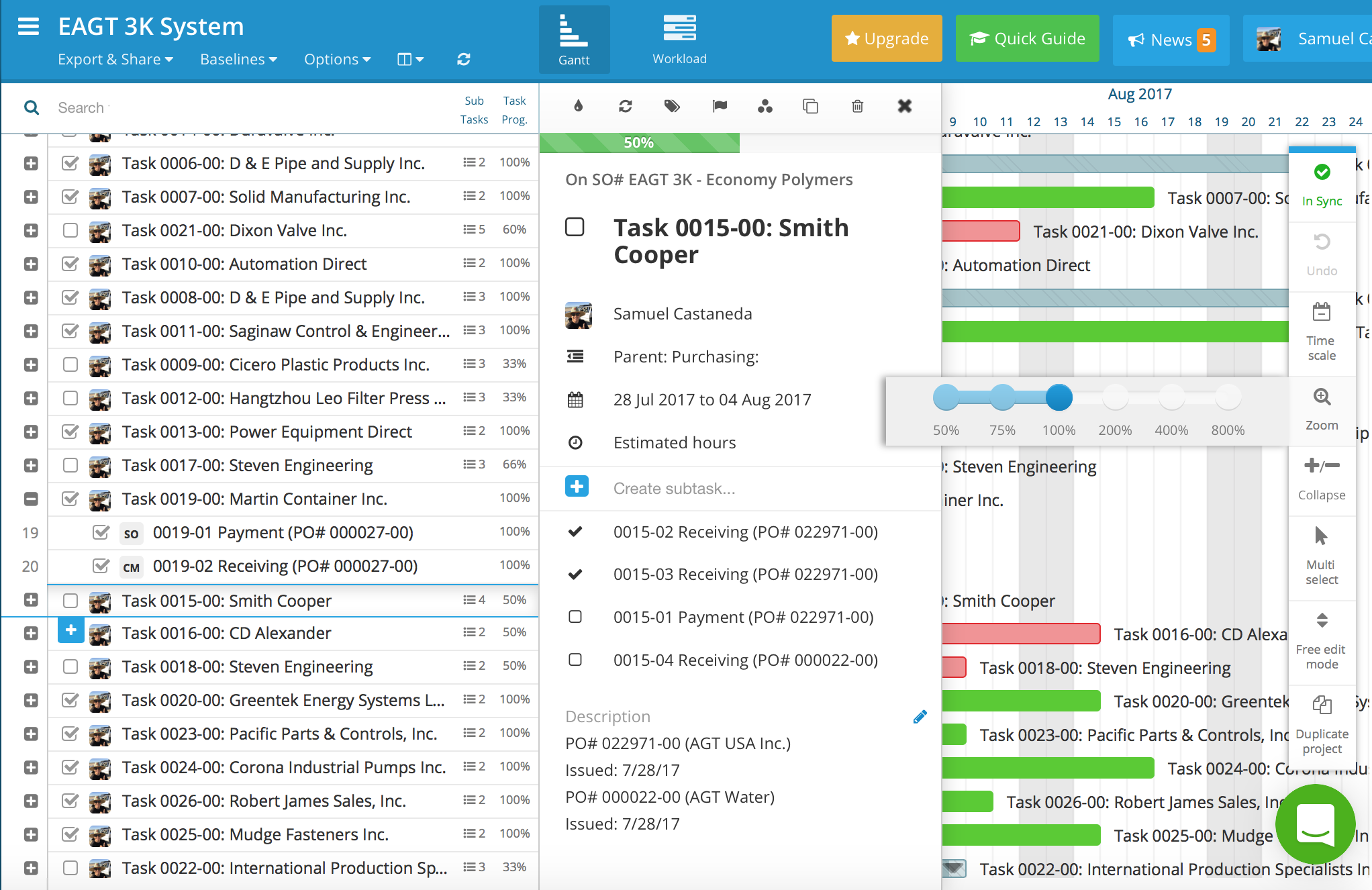
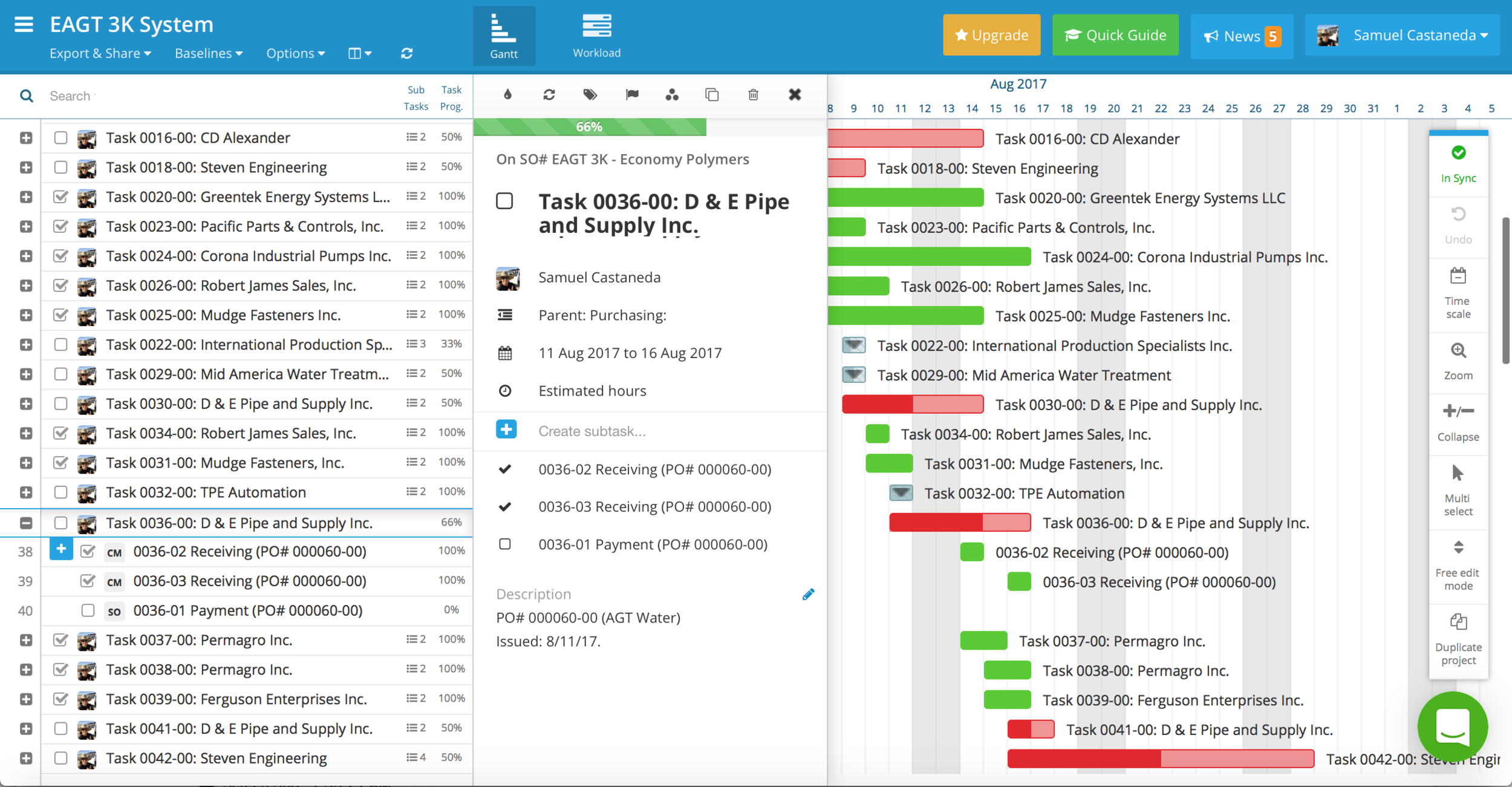
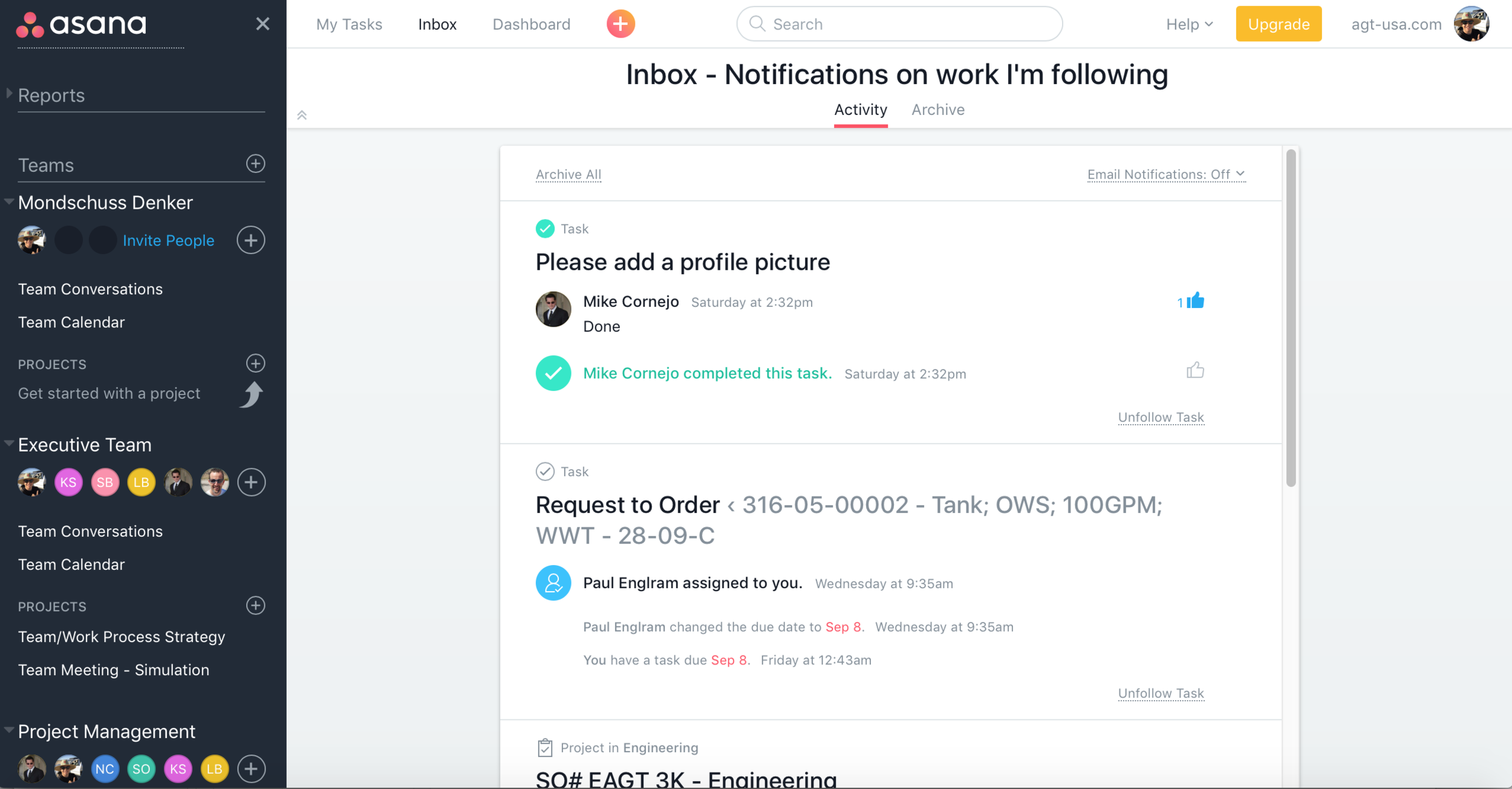
Implementing ASANA
Confident in knowing enough about a few projects, and critical problems in the AGT conglomerate, I test piloted ASANA, and made an effort to experiment with an idea that serves to benefit in several ways. The introduction of ASANA is an end result of the learning experiences acquired abroad the company operations and an attempt to provide a solution to a general problem. The driving vision was to begin project management, establish synchronized communication, and introduce a window of task analysis company wide to drive better decision making and data driven ideas. Having so much information that was not collected from the start of the EAGT3K build, we needed to become more organized for effective manufacturing and with limited resources, limited staff, and a project that still had not been detailed from a design point made it very obvious that the collection of information was important. Using the available information of the EAGT3K project I presented to the executive staff a simulated operation feed for conceptual use of ASANA. Each staff member was provided a test account to explore the ecosystem created and manifest the open canvas platform which was proposed to drive clear and transparent communication. Inside the program there were small project environments and teams created: “Executive Team,” “Project Management,” “Engineering,” and “Production.” This was an effort to begin developing a better communication platform to streamline data, initiate project management tools, and benefit the focused needs of Purchasing, Engineering, and coordinating the Production Floor.
Unsuccessful in acquiring full company integration, the engineering department did start using ASANA as a way to communicate/track progress on BOM development, DWGs, Detailing, Solidworks, Spec Sheet Data, and general correspondence on tasks to accomplish.
Taking the Lead
The fast paced environment to successfully construct, deliver and install a first time prototype is stressful. From the initial start date of production to the very end of the EAGT3K project, data was everywhere to collect and analyze. Having a small set of tools and time, I leveraged my position as the sole procurement officer for AGT Water Systems to independently track financial data, lead times, labor hours, and engineering milestones. Collectively this information was gathered in an effort to plan for future builds and initiate decision making with competent data. Grasping this information directly influenced better procurement, development to the EAGT3K BOM and consolidated system errors (open purchase orders, duplicate part numbers, and faulty parts/design attempts) which all had existed in the material registry. I had put together several documents which were invaluable for future procurement and establishing realistic timelines for the EAGT3K system. In a presentation/report of my findings, the goals were:
Sharing Critical Documents (Gantt Chart, EAGT3K BOM, Purchasing History, and Vendor Analysis)
Review of Critical Procurement Drawbacks
Systematic Plan
Critical Documents
The Gantt chart followed critical milestones found in M2M consisting of date purchase orders were created, payments, and receiving records to show an active story line for procurement purposes of the EAGT3K build. The completed purchasing history report was generated by review of transaction history to each component of the system, noting the highest price we ever paid for certain material (being Vendor 1 as seen in the spreadsheet) to then the cheapest vendor found in sequence and additional sourcing options were provided. The purchasing for the EAGT3K system was conducted all without a sales order to capture the purchasing history so any existing transaction in the system (by part) would be considered directly associated with the EAGT3K project. The raw data provided the cleanest opportunity to capture an accurate cost for the EAGT3K design, reconcile remaining AGT Water inventory, and begin scrubbing the EAGT3K BOM. Being part of the engineering team also meant that I was able to filter the data for faulty parts/design attempts which took place while the build transpired. The purchase information was organized by certain groups: hardware, piping, pneumatic, etc., each having a sum for the overall cost of materials (based on the most expensive price or common price per specific item). Using the available information, I saw a way to circumvent many of the issues experienced under the procurement of the EAGT3K build. Knowing the timelines for most of our procurement needs, I proposed information to initiate early purchasing of time sensitive orders, and consolidate repetitive purchase orders from vendors to make better decisions on pricing and shipping arrangements. From my perspective this had required dedicated analysis of the first EAGT3K BOM and the recorded data could be used to rebuttal against higher priced vendors we used in the past.
Example:
Our first round of RFQ’s for the Butterfly valve [207-03-00006] 3” VALVE; BUTTERFLY;WAFER;BUNA;AIR;3”:
$180.00 - Bray Inc.
$229.25 - Smith Cooper
$271.00 - Bi-Torq
$247.00 - CFM Process Control
About a month after we made the purchase with Bray Inc. for all of the Butterfly valves on the EAGT3K project, I started a dialogue with Bi-Torq on getting better pricing. Having both information and time available to understand where Bi-Torq stood in value before making a material purchase for the upcoming EAGT10K system, Bi-Torq had been renegotiated to obtain all valve business from AGT Water Systems and provide a competitive price break seen below.
$162.60 - Bi-Torq
Critical Procurement Drawbacks
In review of the EAGT3K procurement process the following issues were identified:
Operating out of Google Doc W-MPL (Obsolete)
Assignment of first time part numbers/descriptions with a complicated indexing system
Hand typed RFQ documentation, recording of quote history, pricing, availability of information (all transitioning into ERP system)
First time account set up with vendors
Difficulty acquiring terms/processing credit applications to successfully open an account
Payment procedures, first time payment set up via ACH (72 hr wait time), lack of debit/credit card
Will Call Management
Systematic Plan
The data collected and analyzed provided a foundation to better improve processes all the way around. No longer was the original Google Doc W-AGT MPL being used, and there was now a more streamlined approach for part numbering in addition to a more aggressive use of Made2Manage (ERP software) built in functions to gain better processing time. Having provided a well respected awareness to operational issues and engineering demand, senior leadership relieved me of procurement issues by hiring a direct procurement officer which I trained on our ERP processes for an effective hand off before I stepped into a direct project management/engineering role. Having proprietary knowledge on the ERP system and its foundation, I maintained a direct role managing the ERP system for AGT Water Systems when it came to a liaison between purchasing and engineering. The new procurement officer and I made a goal to be proactive in avoiding procurement delays by having clear awareness to the upcoming needs of projects. While the new procurement officer took the reins on managing procurement requests, my role shifted into full focus toward planning the upcoming 10,000 barrel/day system EAGT10K.
EAGT10k - Project Management
Out of what may be considered critical for project management function, data analysis was secondary to the responsiveness of urgent daily matters in engineering and production. With the launch of the EAGT10K system, the company was expanded to add on two procurement officers to handle the workload I managed solo during the EAGT3K project and a new engineering manager was hired, Priyesh Sharma. Priyesh and I worked together right at the kickstart of the EAGT10K project. Having helped onboard Mr. Sharma to the history of the EAGT3K project, we created a priority for project management objectives while together creating a true BOM, Schematic portfolio, and workflow organization for the EAGT10K project based on the experiences I had with the EAGT3K system.
Project Management Objectives:
Require continuing support of end users and correction of errors with system design
Post implementation review which is a vital phase of learning experience to apply on future projects by analyzing good and bad performance results
Creating infrastructure for the supply of the right information and its update
Communication established on disparities of project parameters
Establishment of KPI indicators into the system
Establishing project structure methods, workflow organization, project control and governance
Transparency establishment
Control systems are needed for cost, risk, quality, communication, time, change, procurement, human resources. Development of process and procedures for how they are implemented effectively
Establishing effective “Tree Structures” to show subdivision of effort required to achieve goals
Work breakdown structure: common framework for overall planning and control of work in definable increments which can be developed into a statement of work developed as schedule, cost, and labor hour reporting
Development of explicit Job orders.