Design for Manufacturing
Note: The following section is academic and exists as a small blueprint for some early impressions made about entrepreneurship and the importance of systems and or the “Franchise Model” to support scalability of knowledge and preserve integrity definitions for product and services. The section is intended as a personal reminder to some creative ideas or interesting “problems” that have yet to be fully explored in my career and anchor my academic interests at-large.
Design for Manufacturing (EAGT3K)
The first manufactured unit for AGT Water Systems was the EAGT3K. A 3,000 barrel/day system that was built through the experience of senior fabricators and electricians working from conceptual schematics. In the course of the first assembled unit, documentation relating to material cost and general milestones was developed. Formal schematics were not available and the real understanding of unit assembly did not take place until after the first EAGT3K system was functioning in the field. Following the 3K system, AGT Water Systems received a contract for a 10,000 barrel/day unit known as the EAGT10K. The two models were very identical aside from volume adjustment, making the majority of vendor and material data from EAGT 3K relevant to the new project. Having a better understanding of the system, I was tasked with profiling the entire EAGT3K assembly. This was achieved through the careful study of photographs taken throughout the entire system. As a completed project, the estimated BOM was cross examined with the overall purchasing list accounting for all purchase orders during the first assembly and used to inform our Solidworks personnel on the correct configurations for the design.
Establishing Project Structures, Workflow organization, governance
We determined that the water filtration system would be best organized by following the modular design between the 6 segmented units: Container 1, Container 2, Container 3, Oil Water Separator (OWS), Clarifier Tank (CL), and Separator Tank (SEP). Each unit was given a master part number starting with “8Z” corresponding to a master assembly. Based on the flow diagram for the 10K system and our reference photos of the EAGT3K project, we determined sub assemblies based on pumps, master lines, electrical panels, sheet metals packages, tanks, and filtration units.
Having the primary insight on the assembly of the unit, I determined the best configuration for BOM construction of the EAGT10K project. All engineering documentation was passed through me for editing and review before adding to the official BOM being constructed for the first time in our ERP system. All drawings were inspected and approved by me before released to the production floor. Knowing also how much time was required for procurement and or custom fabrication work, I was able to pair specific work tasks with an awareness of time and practicality for deadlines assigned.
work breakdown structure
As the engineering team focused on detailing the design of the 10K system, I was studying the construction process and collected data from the EAGT3K system to create a common framework for overall planning and control of work in definable increments which could be developed as a schedule, cost, and labor hour reporting. Creating estimated material cost, labor hours and time commitments for construction was a gateway to discussing strategy not only on the production floor but also in the financial realm of cash flow and investment planning. We had always intended on expanding our manufacturing ability but the pathway was undefined. As a founding team member, it was exciting to be in the midst of planning our work breakdown structure in anticipation for a much larger order queue in the next fiscal year 2019.
job orders
The ERP system was not used to its’ full capacity during the first two production cycles of AGT Water Systems. Our manpower and effort was focused on creating a functioning unit and documenting the system. In the midst of the EAGT10K system planning we decided to implement job orders and allocated work instructions based on the defined parameters of schematic packets. In tandem, the purchasing agency worked alongside shipping to reorganize physical inventory through the ERP system and cage the inventory for approved personnel only. The pressure to successfully meet a project deadline, implement newly developed job orders and maintain order through the adjustment period for inventory controls caused a lot of tension between production floor staff, engineering, procurement, and executive staff. I learned that process was valuable, but there was an appropriate time and place for everything. AGT Water Systems was a subsidiary to a business operating for over 20 years in the refrigeration industry. Their senior staff had manufactured cooling systems for the printing industry without the systematic management of an ERP system, nor an engineering and procurement team dictating release of job orders. Our main directives for new process was through the will power of our CFO who was trying to encourage stable working practices for balancing the financial challenge of managing overhead of a decaying product line (AGT’s core refrigeration business) and the upstart demand for AGT Water Systems.










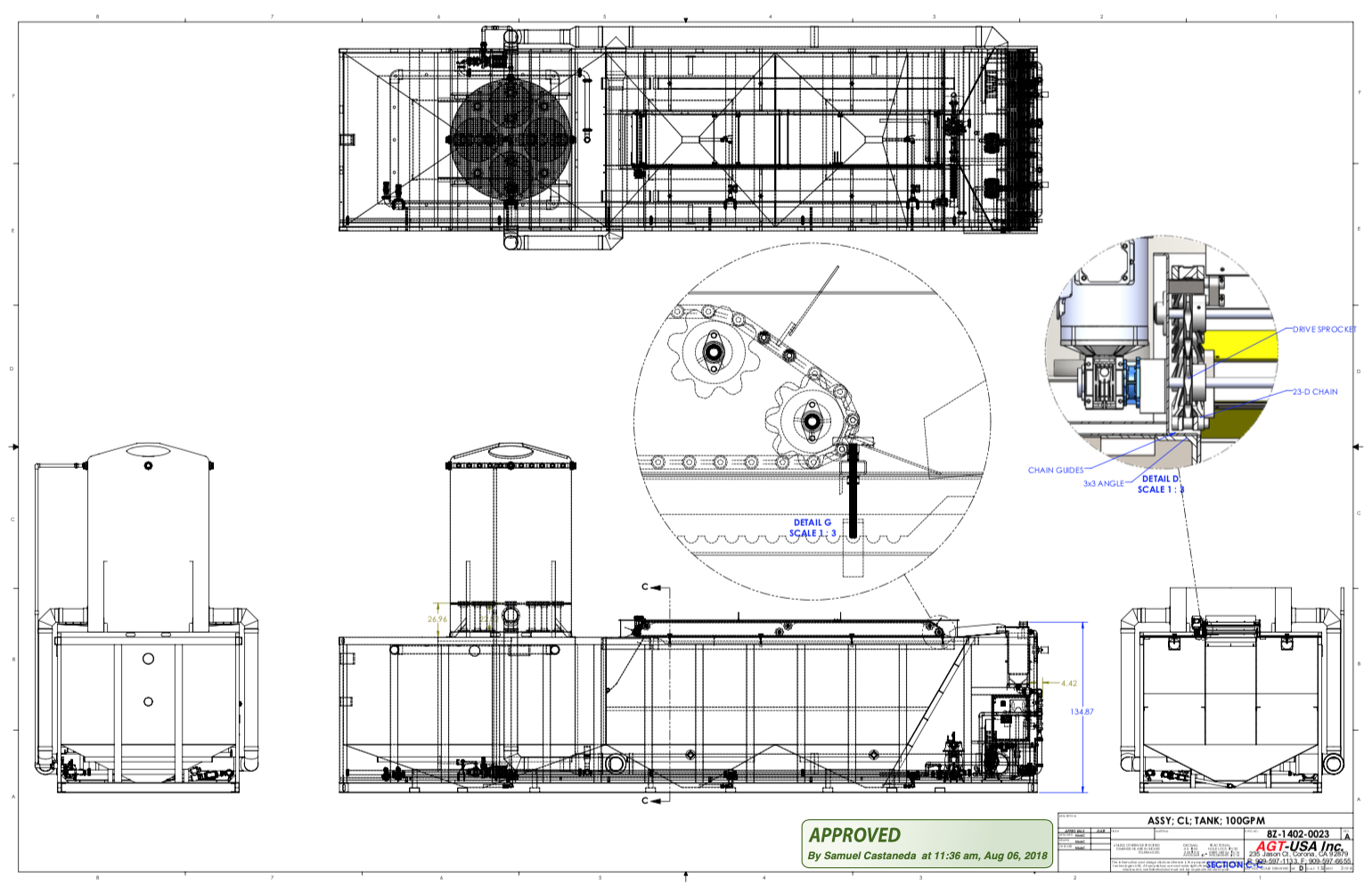

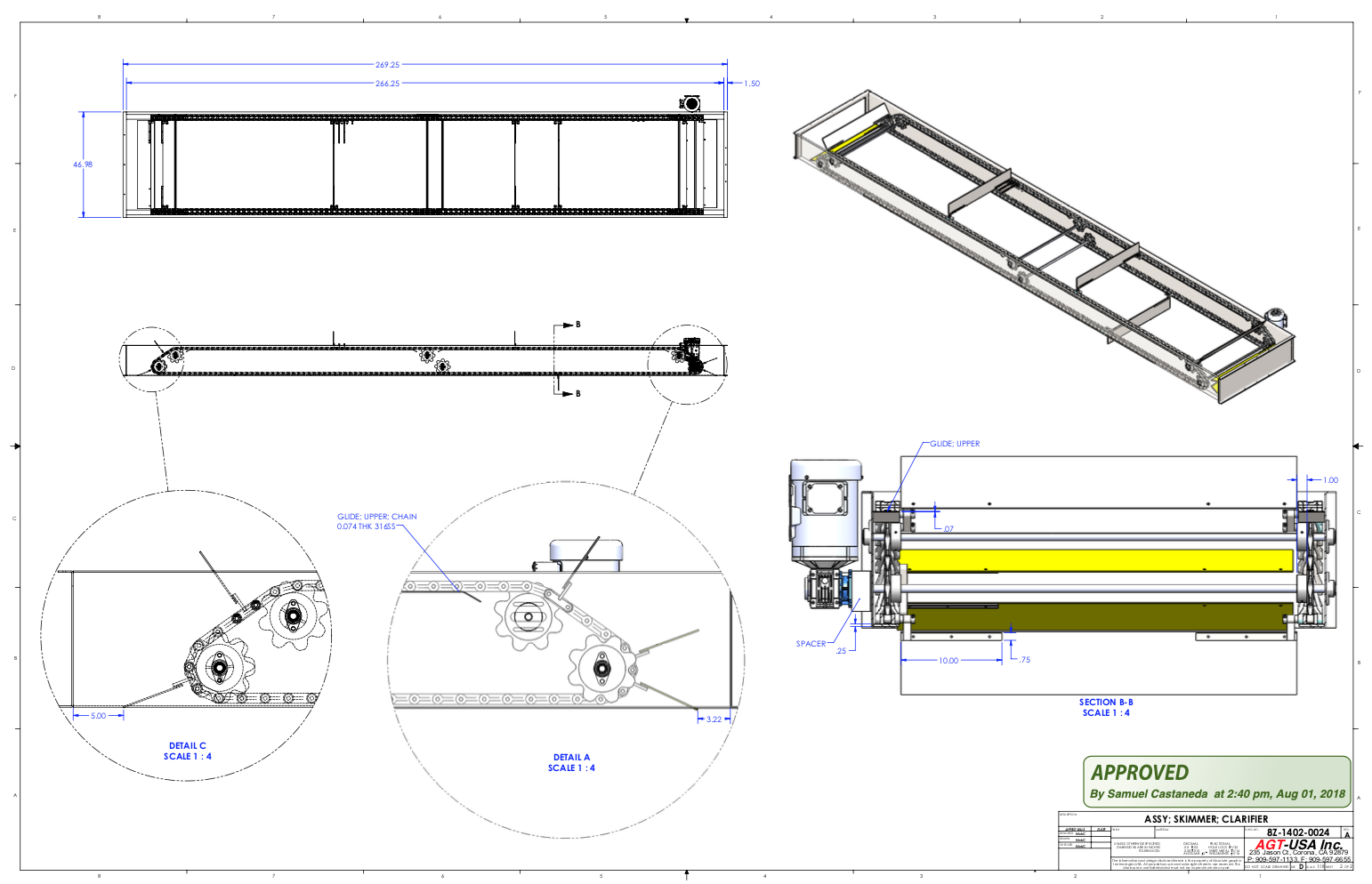
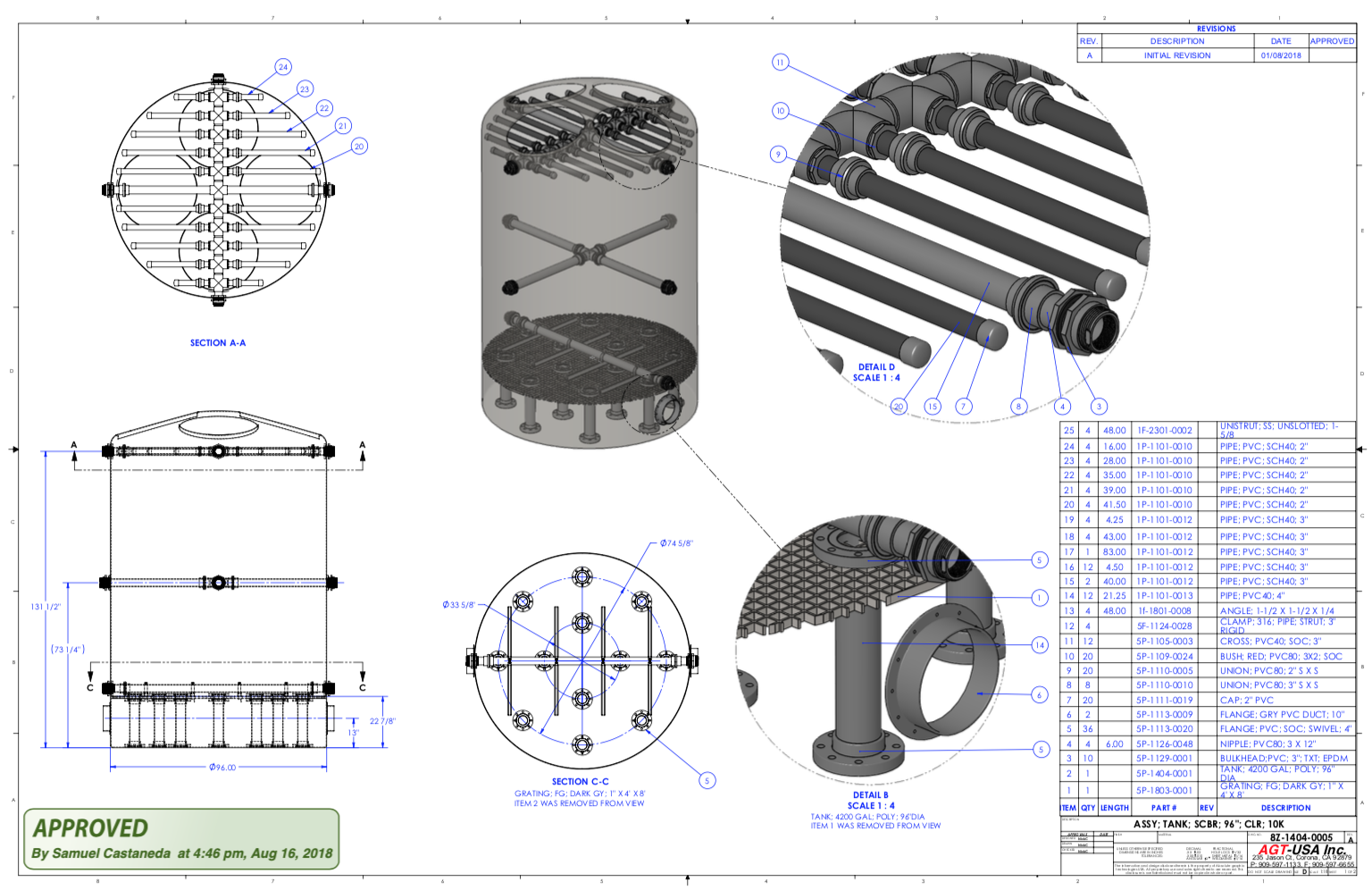

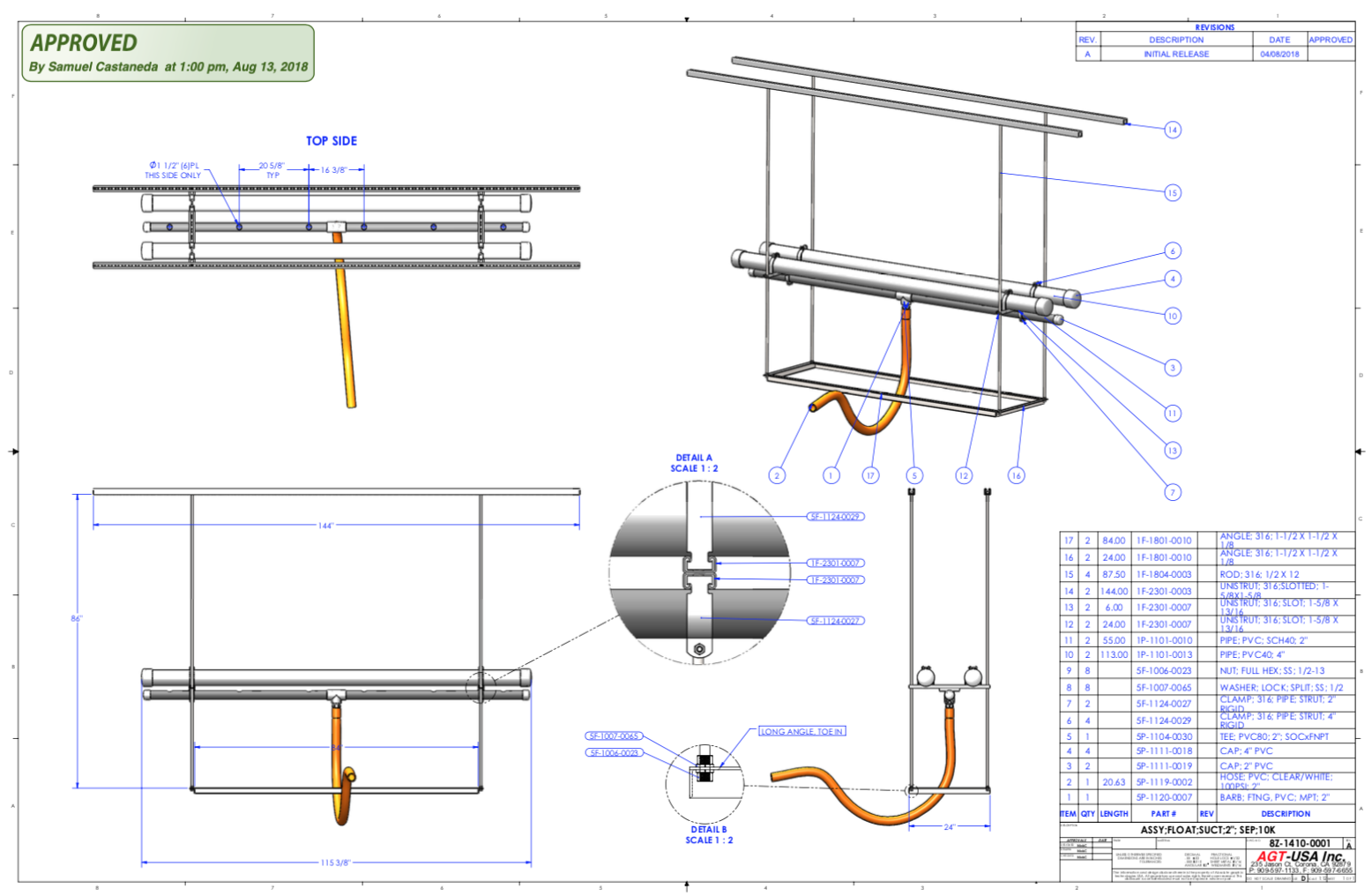
Engineering Management (WRX1200)
I was introduced to engineering management and design for manufacturing here at Webber Automation. Our technical team was very entrepreneurial in their product design and fabrication. I was given my first time experience with Solidworks/Inventor and design for manufacturing concepts at Webber Automation for a complete machine assembly. Some of the major accomplishments while working at Webber Automation were as follows:
File Management, creating effective processing for engineering and design
Redesign of system with sub assembly organization
Created production timeline
Marketing development (www.webberautomation.com)
As a best practice, I learned to set parameters for technical objectives and communicate on progress towards weekly and monthly goals. The creative edge of engineering and inventor personalities was an extraordinary insight into technical creativity and inspired a career path towards enabling innovation by preserving organizational structure and finance to initiatives. In this experience I learned about the amazing ability engineers and inventors possess but their talents often need a sense of structure in order to maintain the longevity of the organization. The profitability in Webber Automation was difficult to protect because constant revision and new design concepts were taking place while trying to accomplish a completed unit by the given deadlines. I learned a lot in this time about the challenges behind forming a company and finding a path towards sustainable growth in entrepreneurship. it has been a valuable memory that any design phase for a product must find a conclusive end.
CREATING EFFICIENT FABRICATION
Without a formal fabrication design, signature PLC's and Pasteurizers of Specialized Dairy Service were created by an assorted group of technicians running in and out of the shop often to handle other responsibilities. As one of the first projects I tackled at SDS, all fabricated products were studied to create comprehensive build templates and AutoCAD Documentation.